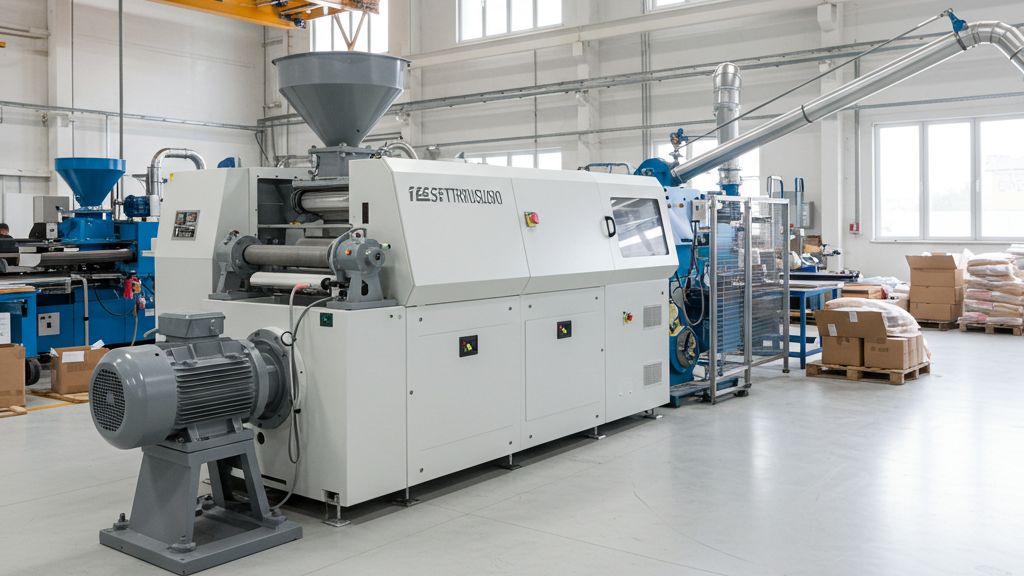
ABS material is widely used in several industries due to its durability and ease of processing. In order to get the most out of its performance, it is essential to choose the right machining process.
This article will briefly introduce the main processing methods of ABS materials to help you understand how to choose according to your needs. Mastering the basic principles of these processes can help us make better use of ABS materials to create products that meet the requirements.
What is the most common processing process for ABS materials?
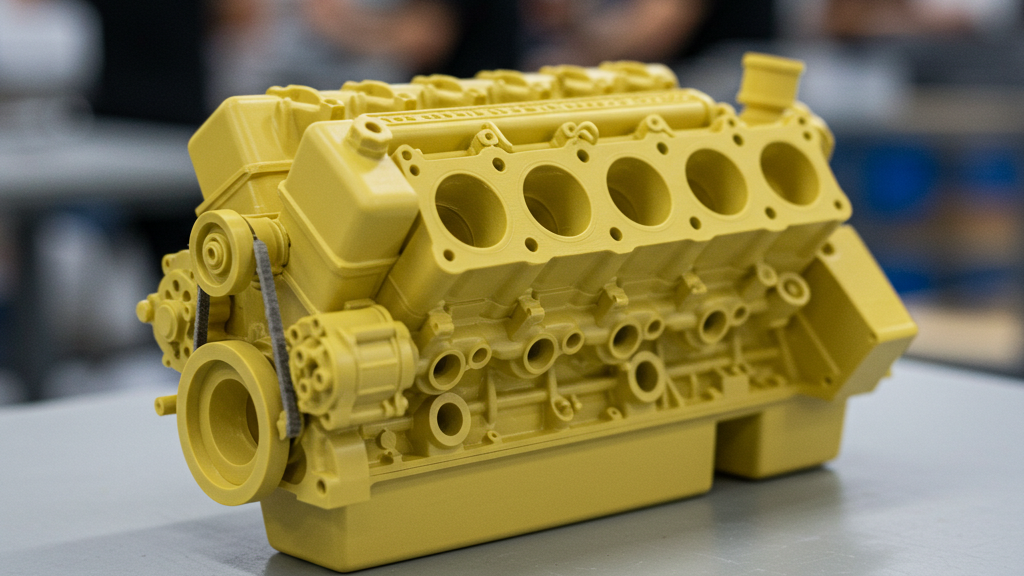
From everyday products to industrial components, ABS materials are everywhere. The processing technology behind it is the key to the versatility and functionality of these products.
- Injection molding: Manufacture of ABS parts with complex shapes with high efficiency through molds.
- Extrusion: Production of continuous ABS profiles such as tubes and plates.
- Vacuum forming: Vacuum adsorption is used to form ABS sheets into thin-walled parts.
- 3D printing: Complex ABS 3D structures are fabricated by stacking them layer by layer.
What is the impact of different processes on the performance of ABS materials?
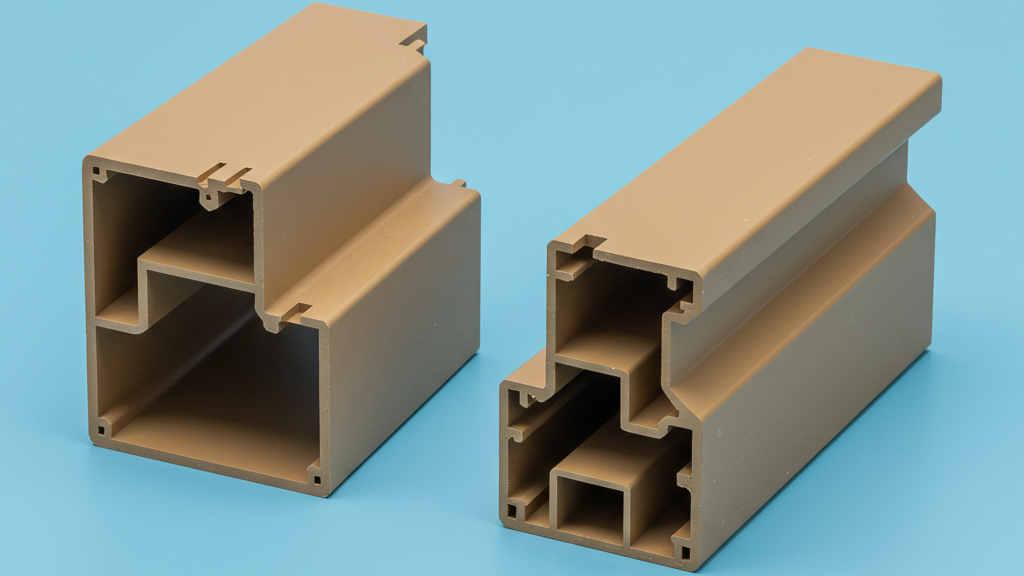
From rugged automotive parts to intricate electronics housings, ABS materials exhibit a wide variety of properties in different fields. And all this is inseparable from the various processes that process it.
- Injection molding: Optimize the strength and surface finish of ABS materials by controlling parameters.
- Extrusion: It mainly affects the continuity and uniformity of ABS materials, and the mechanical properties of the materials will be affected by the extrusion process.
- Vacuum forming: It will affect the thin-wall uniformity and surface fit of ABS material, and it will have a certain impact on strength.
- 3D printing: Affecting the interlayer adhesion and surface quality of ABS materials, printing parameters are the key to affecting the properties of materials.
What factors should be considered when choosing an ABS material process?
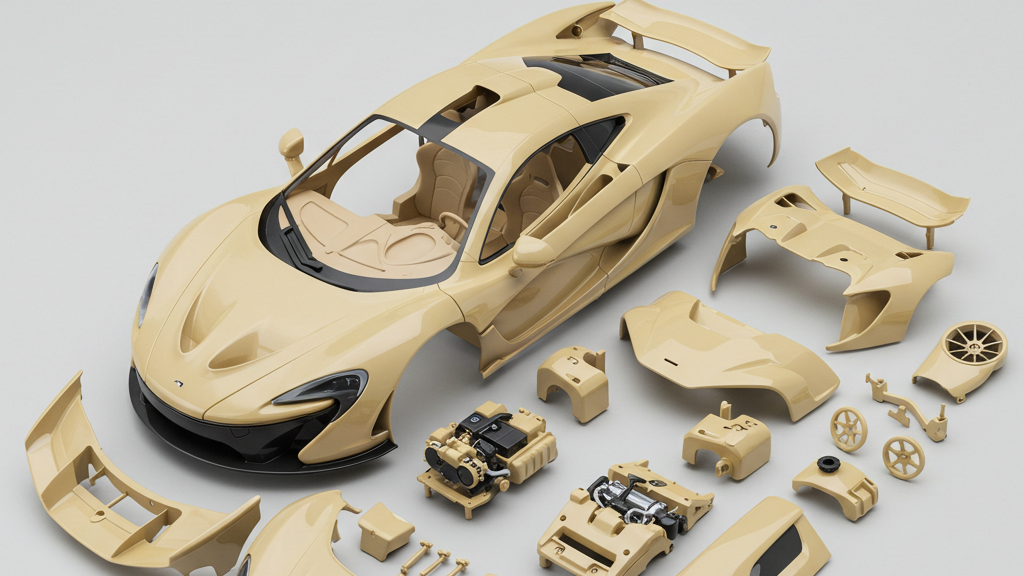
Each ABS material processing process has its own unique advantages and limitations. Choosing the right process can not only ensure the quality of the product, but also effectively control the production cost.
- Product design and requirements: select the most suitable processing technology according to the shape complexity, dimensional accuracy, surface quality and mechanical properties of the product.
- Production scale and cost: Weigh the economics of different processes based on batch size, tooling cost, and material utilization.
- Material performance requirements: According to the use environment of the product, select the processing technology that can meet the requirements of heat resistance, impact resistance and chemical resistance.
- Environmental protection and sustainability: Consider waste disposal and energy consumption, and choose more environmentally friendly processing methods.
Comparison of common processing technology and performance of ABS materials
Processing Technique |
Key Features |
Advantages |
Disadvantages |
Performance Impact |
Applicable Scenarios |
Injection Molding | Efficient, precise, suitable for complex shapes | High output, high precision, good surface finish, adjustable mechanical properties | High mold cost, not suitable for small batch production | Strength, surface finish, internal stress | High volume production, complex parts, high precision products |
Extrusion Molding | Continuous production of profiles, such as pipes and sheets | High production efficiency, suitable for long or sheet products | Shape limitations, potential for orientation affecting mechanical properties | Continuity, uniformity, mechanical properties | Continuous products such as pipes, sheets, and profiles |
Vacuum Forming | Heating and softening sheets, adsorption forming | Low cost, suitable for large thin-walled parts | Low precision, uneven thickness | Thin-wall uniformity, surface conformity, strength | Thin-wall housings, packaging, large covers |
3D Printing | Layer-by-layer stacking, creating complex 3D structures | No mold required, suitable for small batch, customized production, complex geometries | Slow speed, weak interlayer bonding, surface quality requires post-processing | Interlayer bonding, surface quality, mechanical properties | Small batch customization, prototyping, complex parts |
ABS materials and emerging processing technologies
As a widely used engineering plastic, the combination of ABS material and emerging processing technology has brought new opportunities and challenges to the manufacturing industry. With the continuous advancement of technology, ABS materials will play an important role in more fields.
1.3D printing (additive manufacturing): ABS materials can be customized through 3D printing, but they need to overcome the challenges of interlayer adhesion and surface quality.
2.Intelligent manufacturing: Integrating sensors and big data, ABS material processing is developing towards automation, efficiency and intelligence.
3.New processing technology: Emerging processes such as laser sintering expand the accuracy and application range of ABS materials.
conclusion
ABS materials are used in a variety of processing processes to achieve diversified applications, and the selection of appropriate processes needs to comprehensively consider product requirements, cost and performance. Emerging technologies such as 3D printing and smart manufacturing have brought innovation to ABS material processing and promoted its development in more fields.
For expert assistance in implementing for your production needs, visit our resource center or contact us. Let’s help you scale up your manufacturing with precision and efficiency!
Post time: Mar-14-2025