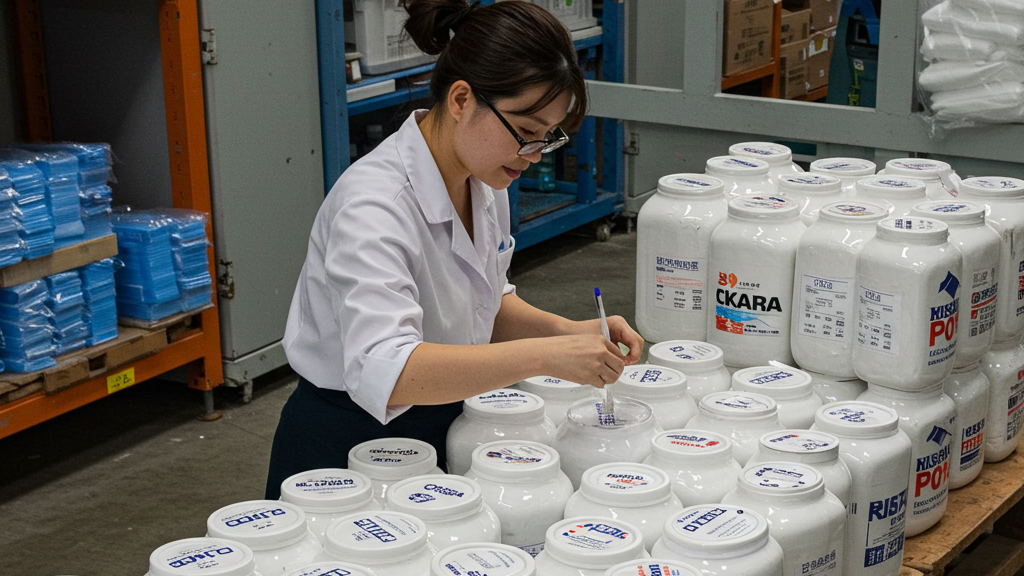
Blow molding is an important process for manufacturing hollow plastic products, and blow molds are at its core. The suitability of the mold directly affects product quality and production efficiency. So, which plastic products are suitable for production using blow molds? This article will explore the types of plastics suitable for blow molds and their wide applications from a professional perspective, revealing their value in industrial production.
As can be seen, blow molds have significant advantages in producing plastic products of specific shapes, with applications ranging from packaging to industrial components. Different plastic materials have different characteristics, and their performance in blow molding varies. Next, we will focus on several common blow molding plastics, analyzing their advantages and considerations in practical applications.
Which Plastic Materials are Suitable for Blow Molding?
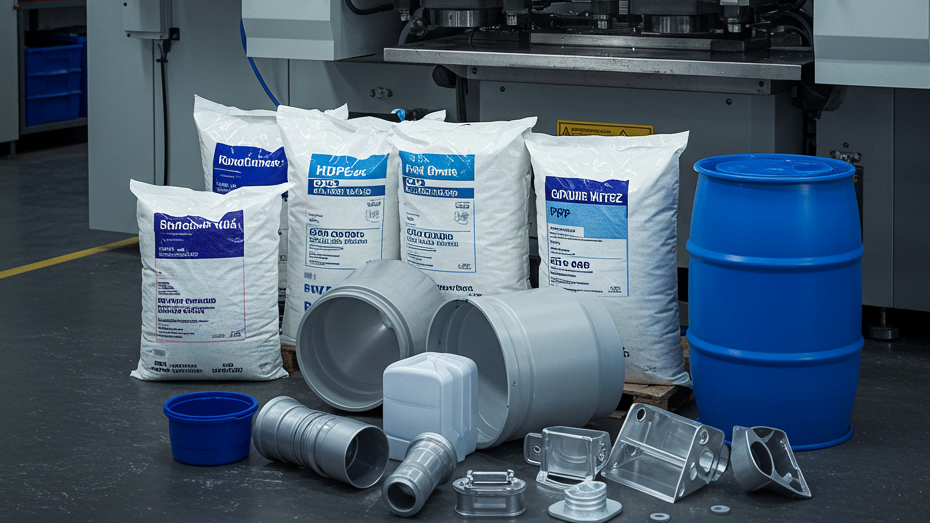
Key material properties such as melt strength, ductility, and cooling shrinkage directly determine the suitability of a plastic for the blow molding process and the quality performance of the final product.
- High-Density Polyethylene (HDPE): Excellent melt strength and rigidity make HDPE an ideal choice for producing various bottles, jars, and industrial containers.
- Polypropylene (PP): Good chemical stability and moderate melt strength allow PP to be widely used in the blow molding of food, pharmaceutical, and automotive components.
- Polyvinyl Chloride (PVC): Good plasticity and a low melting temperature make PVC easy to blow mold into complex shapes.
- Polyethylene Terephthalate (PET): High tensile strength and transparency make PET particularly suitable for producing transparent packaging containers that need to withstand pressure.
What are the Advantages of Blow Molds in the Production of Products for Different Uses?
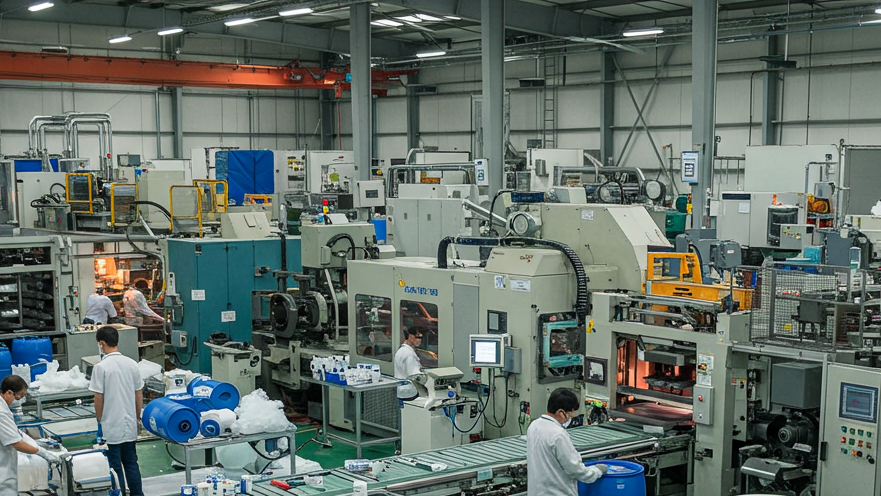
Blow molds can flexibly adapt to the functional requirements of plastic products in different industries. Through structural design and process adjustments, they can achieve goals such as lightweighting, sealing performance, or specific mechanical properties.
- Design Flexibility and One-Piece Molding: The blow molding process can integrally manufacture products with complex shapes and structures, reducing assembly steps.
- Lightweighting and Cost-Effectiveness: Blow molding often uses less material to achieve lightweighting, thereby reducing production costs.
- Good Sealing Performance: Precise mold design enables blow-molded products to have excellent sealing performance, ensuring product quality and safety.
- Adaptability to Various Materials and Special Properties: Blow molds can use a variety of plastics and give the product specific functionality.
What are the Unique Features of Blow Molds in the Production of Specific Shaped Products?
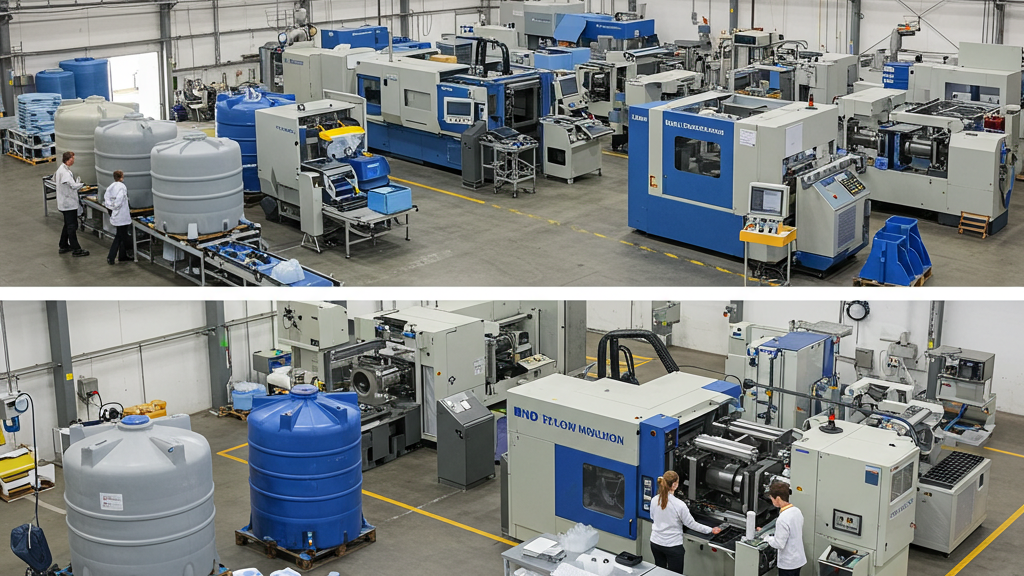
The blow molding process can economically and efficiently produce integrated closed or semi-closed cavity structures, avoiding the need for multiple parts to be injection molded and then assembled, as might be required in traditional processes.
- Ability to Manufacture Hollow or Tubular Structures: Blow molds are adept at efficiently producing various hollow or tubular plastic products.
- One-Piece Molding of Complex Irregularly Shaped Parts: The blow molding process can form products with complex contours and internal spaces in a single step.
- Production of Large Thin-Walled Parts with Good Wall Thickness Uniformity: Blow molding can better control wall thickness uniformity when manufacturing large thin-walled containers.
- Achieving Overmolding and Multi-Layer Co-Extrusion Blow Molding: Special blow molding processes can combine different materials to manufacture products with special functions or appearances.
Overview of application fields of blow molding dies
Application Field |
Common Plastic Product Types |
Common Plastic Materials |
Blow Molding Advantages |
Packaging Industry | Beverage bottles (water, carbonated drinks, juice), edible oil drums, detergent bottles, cosmetic bottles, medicine bottles, food jars, etc. | PET, HDPE, PP, PVC | Lightweight, cost-effective, good sealing performance, can achieve complex shape designs |
Automotive Industry | Automotive fuel tanks, ventilation ducts, coolant expansion tanks, bumpers, dashboard components, seat backs, etc. | HDPE, PP, PA, TPO | Production of large, uniquely shaped hollow parts, lightweight design, corrosion resistance, meeting strength requirements |
Medical Industry | Medical reagent bottles, infusion bottles, drainage bags, ventilator tubes, artificial organ models, etc. | LDPE, PP, PVC, Medical Grade Plastics | High hygiene and safety requirements, can produce containers of different capacities and shapes, some can achieve transparency or translucency, meeting specific biocompatibility |
Household Goods | Trash cans, storage boxes, toys, gardening tools (watering cans, flower pots), furniture parts, etc. | HDPE, PP, LDPE | Production of large or uniquely shaped hollow products, low cost, good durability, diverse colors and designs |
Industrial Products | Chemical containers (acid and alkali barrels), toolboxes, floats, traffic barriers, large hollow components, etc. | HDPE, PP, PVC, Modified Plastics | Corrosion resistance, high strength, can produce large containers, meeting the specific requirements of industrial environments |
Other Fields | Sports water bottles, children’s seats, buoyancy aids, lampshades, musical instrument shells, etc. | PC, ABS, HDPE, PP | Flexible design, meeting specific functional requirements (such as impact resistance, transparency), diverse colors and appearances |
Application Potential in Emerging Fields
With the continuous emergence of new materials and the ongoing innovation of blow molding technology, blow molds will demonstrate enormous application potential in more emerging fields of plastic product production. The development of personalized customization and intelligent manufacturing will also promote the evolution of blow molds towards greater flexibility and intelligence, to meet the production needs of small-batch, customized, and high-performance plastic products.
- Biodegradable and Environmentally Friendly Material Products: Blow molds will play a key role in the production of environmentally friendly plastic products, especially in replacing single-use plastics.
- Flexible Electronics and Wearable Devices: Blow molding technology is expected to be used to manufacture housings and substrates for flexible electronic devices, enabling lightweight and bendable designs.
- Personalized Medical and Biopharmaceutical Products: Blow molds will be used to produce customized medical devices and complex scaffolds for tissue engineering.
- Lightweight and High-Strength Composite Material Products: Combining advanced technologies, blow molds can be used to manufacture lightweight, high-strength components in fields such as automotive and aerospace.
Conclusion
Blow molds are crucial in plastic product manufacturing due to their unique advantages and material adaptability. They are widely used in industries such as packaging, automotive, medical, and industrial, producing various critical components. Blow molds will play an even more important role in future plastic product production, providing efficient, economical, and environmentally friendly solutions.
For expert assistance in implementing for your production needs, visit our resource center or contact us. Let’s help you scale up your manufacturing with precision and efficiency!
Post time: May-14-2025